Hairpin motor welding
Electric vehicle motors are an important part directly related to vehicle performance and energy efficiency. The hairpin-shaped design provides higher torque and output compared to ROUND WIRE as a solution to reduce interference. Since copper bars with both ends removed must be wound and inserted in a U-shape, precision system design is essential.
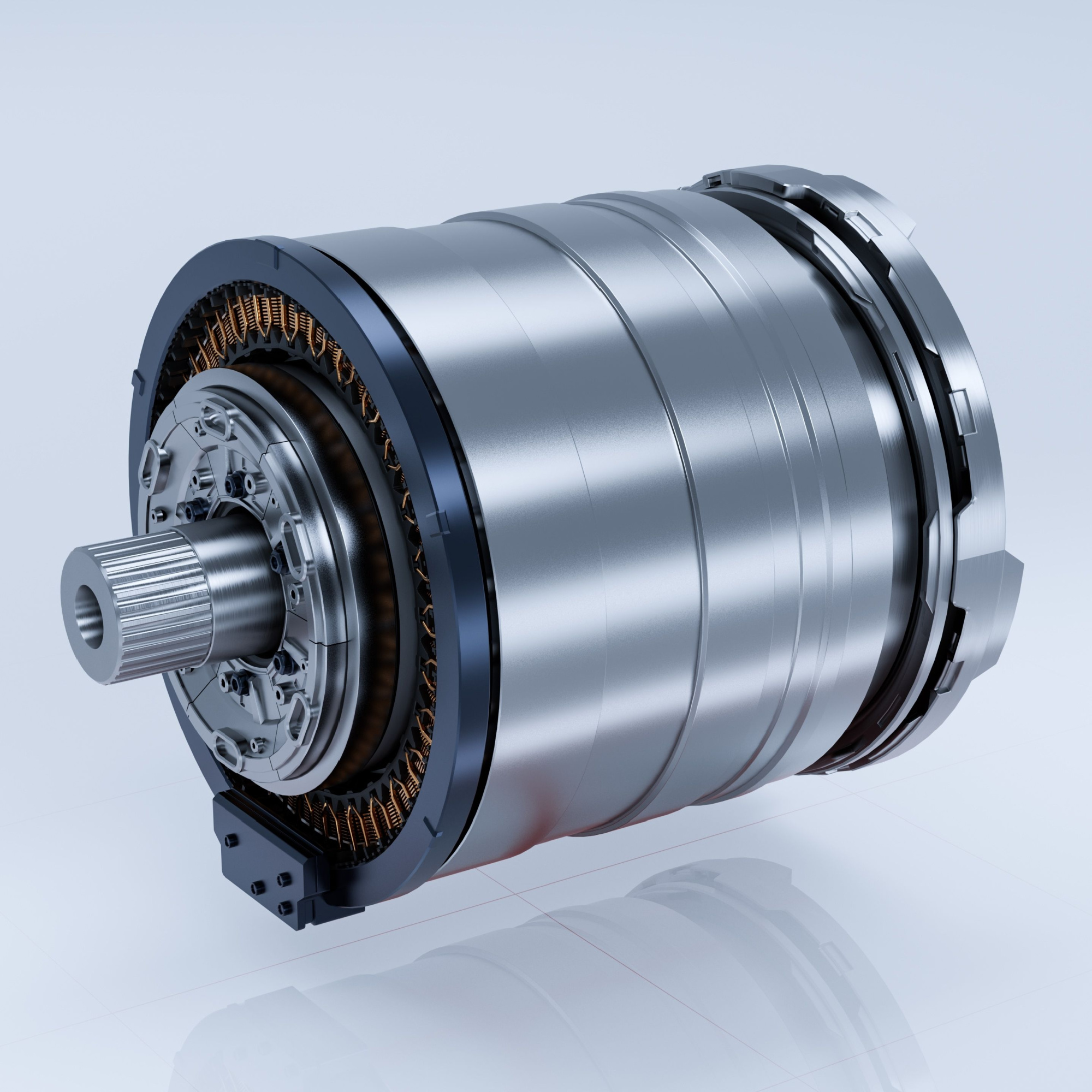
Features
STRIPPING
Pulsed energy is used to remove the enamel insulation layer. Color deformation due to thermal effects does not cause structural changes in copper, but it can cause peripheral contamination and malfunction due to Burr. Lasers perform ablation and cleaning 80% faster than mechanical methods.
Marking
Tracking marks, including text, logos, barcodes, and serial numbers, can be finely engraved on the stator surface. Production quality can be properly controlled by tracking raw materials and finished products with permanent laser engraving.
WELDING
The protruding part of the hairpin inserted into the stator is welded by Pair. In order to prevent weld defects caused by vehicle vibration, it is necessary to reduce external changes and warpage due to melting. Laser systems with precise targeting and flexible position changes can implement excellent welding methods such as wobble and cross machining.
STRIPPING
Pulsed energy is used to remove the enamel insulation layer. Color deformation due to thermal effects does not cause structural changes in copper, but it can cause peripheral contamination and malfunction due to Burr. Lasers perform ablation and cleaning 80% faster than mechanical methods.
Marking
Tracking marks, including text, logos, barcodes, and serial numbers, can be finely engraved on the stator surface. Production quality can be properly controlled by tracking raw materials and finished products with permanent laser engraving.
WELDING
The protruding part of the hairpin inserted into the stator is welded by Pair. In order to prevent weld defects caused by vehicle vibration, it is necessary to reduce external changes and warpage due to melting. Laser systems with precise targeting and flexible position changes can implement excellent welding methods such as wobble and cross machining.
3kW
MULTI
Core Technology
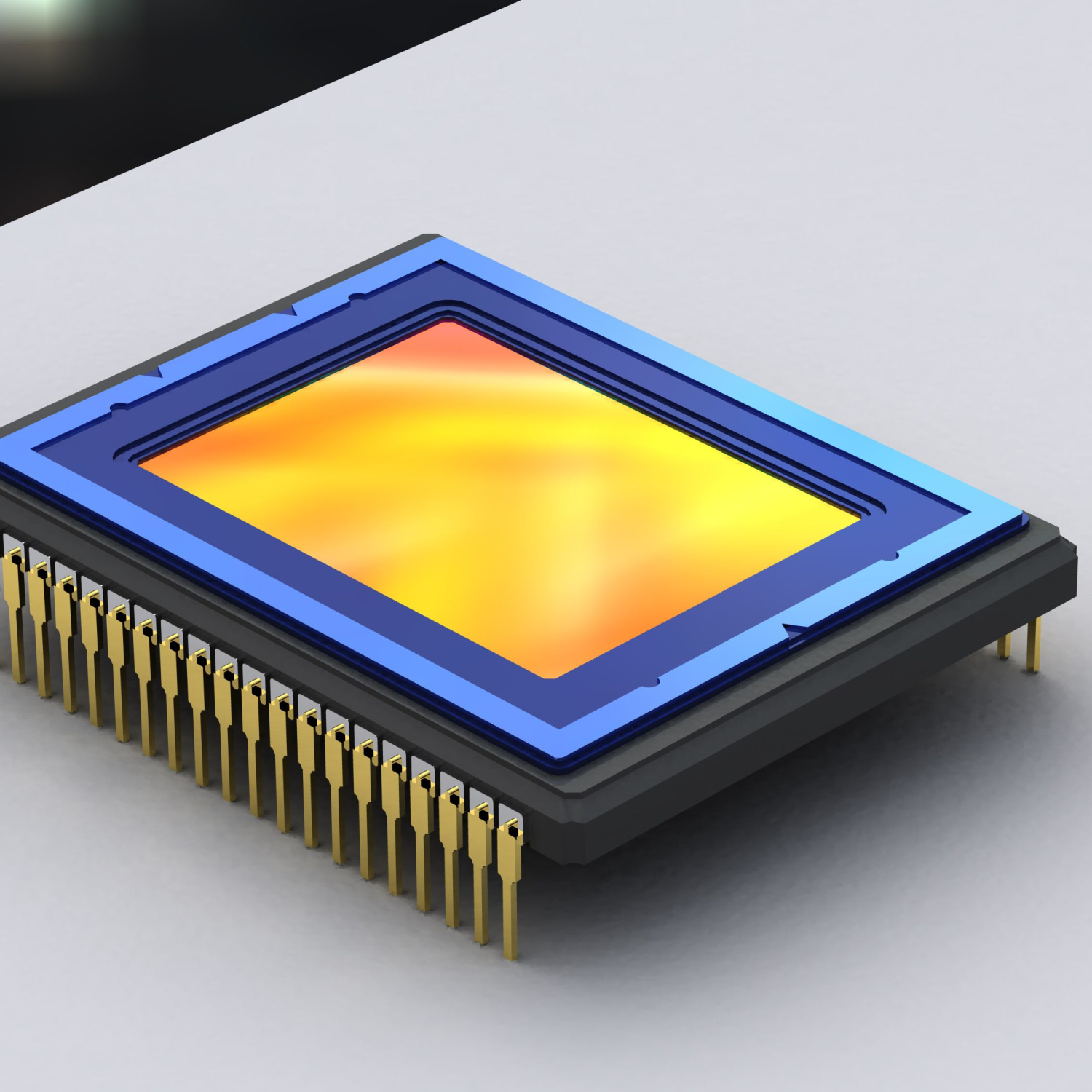
OCT
For excellent processing accuracy, hairpin errors generated during the entire process must be precisely measured. OCT is a proven method for detecting the height and position of hairpin pairs. If the allowable tolerances are exceeded, welding is not performed and unnecessary consumption of materials is prevented. Furthermore, by measuring the outline of the solidified weld bead with OCT, it is possible to automatically detect defects in the bead and reduce conductivity degradation.
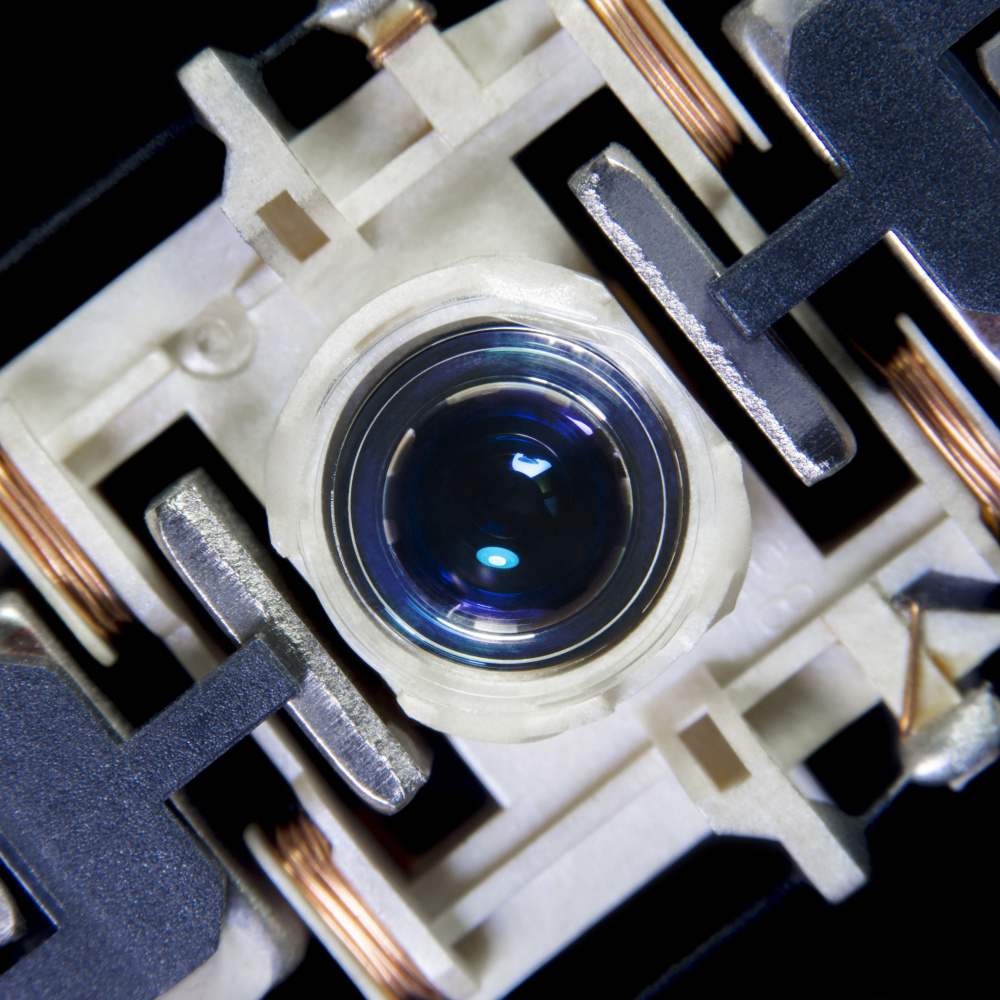
SMART Alignment
To achieve full weld quality while minimizing processing time, hairpins must be properly aligned. K2's Hairpin welding system measures the shape and relative position of the hairpin before processing is performed to check for gaps, gaps, and inclinations.
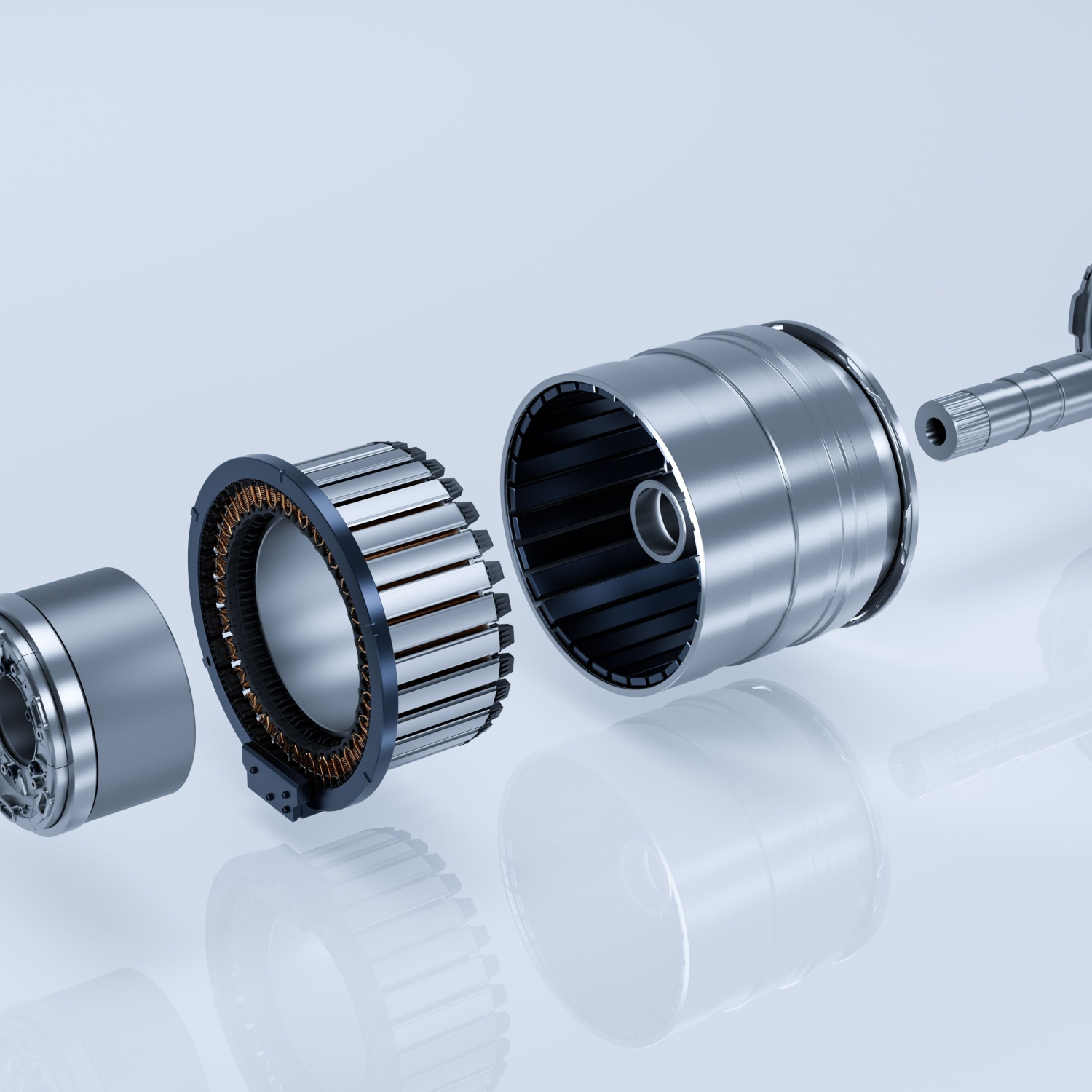
Superb quality
Various core capabilities must be fully implemented in laser peeling and laser welding equipment for hairpin motors, such as jig fixing systems, pore suppression technology, and pollution minimization structures. Join K2Laser, a laser expert
Core Technology
Heading
Lorem ipsum dolor sit amet, consectetur adipiscing elit. Suspendisse varius enim in eros elementum tristique. Duis cursus, mi quis viverra ornare, eros dolor interdum nulla, ut commodo diam libero vitae erat. Aenean faucibus nibh et justo cursus id rutrum lorem imperdiet. Nunc ut sem vitae risus tristique posuere.
Heading
Lorem ipsum dolor sit amet, consectetur adipiscing elit. Suspendisse varius enim in eros elementum tristique. Duis cursus, mi quis viverra ornare, eros dolor interdum nulla, ut commodo diam libero vitae erat. Aenean faucibus nibh et justo cursus id rutrum lorem imperdiet. Nunc ut sem vitae risus tristique posuere.
Heading
Lorem ipsum dolor sit amet, consectetur adipiscing elit. Suspendisse varius enim in eros elementum tristique. Duis cursus, mi quis viverra ornare, eros dolor interdum nulla, ut commodo diam libero vitae erat. Aenean faucibus nibh et justo cursus id rutrum lorem imperdiet. Nunc ut sem vitae risus tristique posuere.
Heading
Lorem ipsum dolor sit amet, consectetur adipiscing elit. Suspendisse varius enim in eros elementum tristique. Duis cursus, mi quis viverra ornare, eros dolor interdum nulla, ut commodo diam libero vitae erat. Aenean faucibus nibh et justo cursus id rutrum lorem imperdiet. Nunc ut sem vitae risus tristique posuere.