Precision Laser Process
The overwhelming productivity of laser precision processing technology is driving manufacturing innovation. We will listen to the unique voices of our customers and implement them as solutions so that we can stay ahead of the competition.
The most effective optical system design completes welding solutions for demanding material processing applications.
High-precision work is performed at high speed according to the movement of materials. Increase productivity with reliable and active control technology.
A consistent array is processed according to a finely designed pattern. The process is performed without material deformation using techniques optimized for material and thickness.
Removes the surface layer of parts finely and completely. Non-contact cleaning without residue enhances the quality of the post-process.
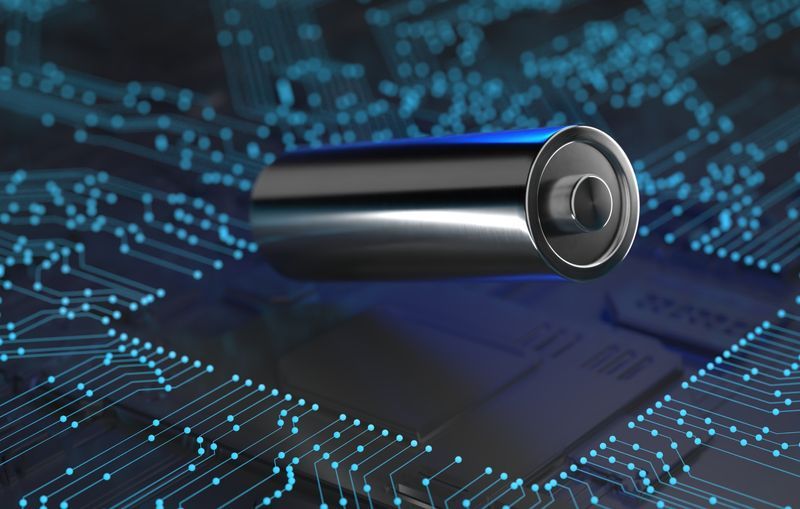
Continuing efforts for technological innovation
Complete implementation of specialized solutions
Defining requirements
Process design
Facility design
System implementation
Ongoing care
Optimal process systems

Machine systems
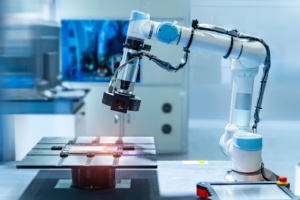
Optical metrology
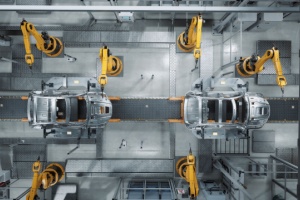
Automation control
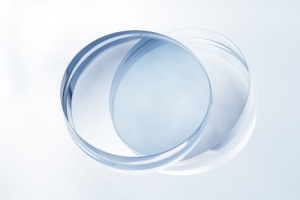
beam shaping
K2 blog
장치 구성, 가공 노하우, 공정 설계 등 레이저 시스템 전반에 대한 포스트를 업로드합니다.