Material process analysis
Research on new system configurations and processing techniques must be carried out every time there is a constant change in materials to improve quality and efficiency. MATERIAL PROCESSING tracks and analyzes various aspects of deformation due to laser processing from research on raw materials so that defect-free processing solutions can be proposed. (eg. Contamination level, impurity distribution, cross-sectional profiling, particle and crystal structure, quality reliability, etc.)
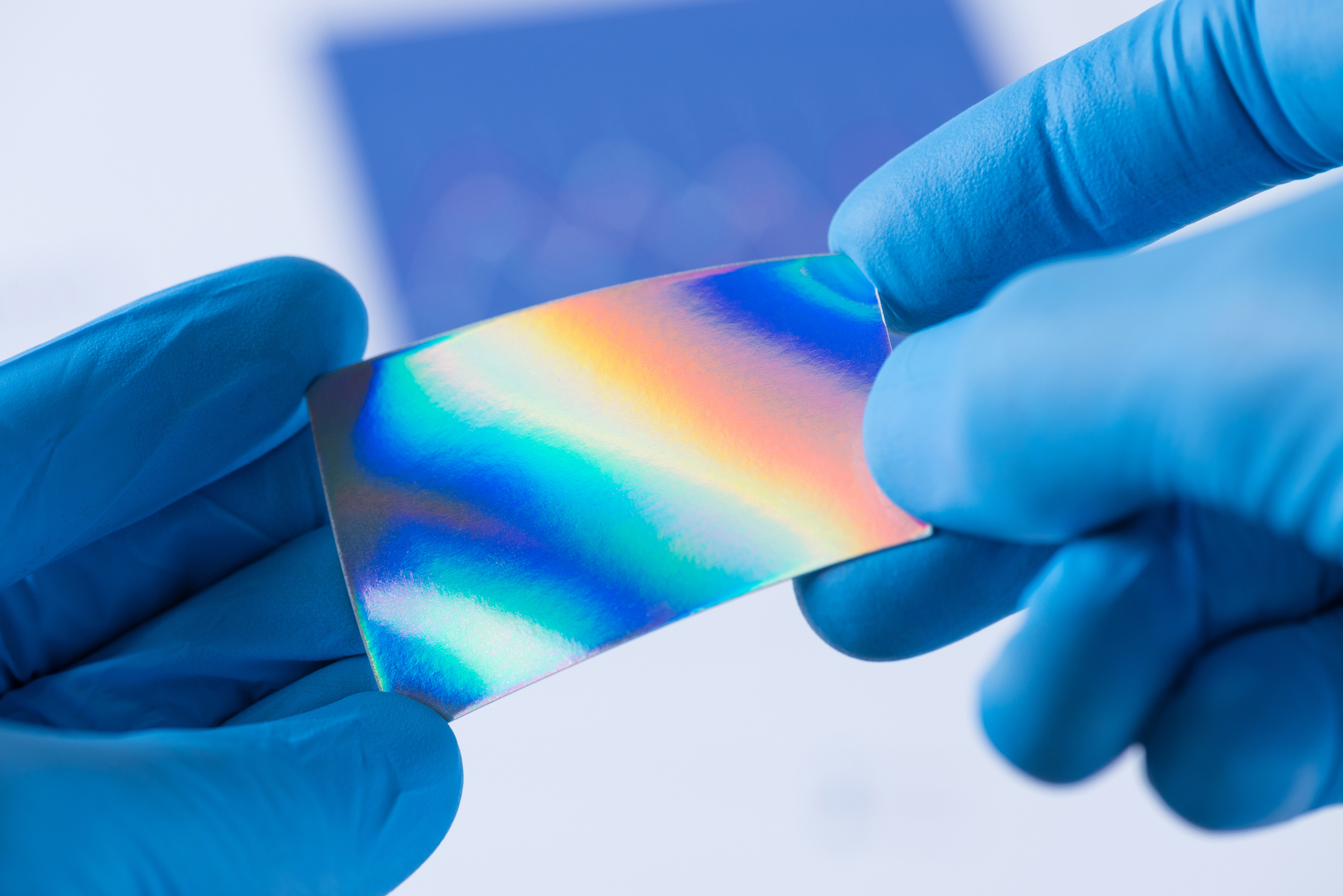
Features
Feasibility study
The materials and applications to be processed are analyzed to evaluate whether the customer's desired process program can be implemented with a laser and operated efficiently.
Responsiveness assessment
When lasers and other external stimuli are applied, the response of materials and devices is monitored, and the modified area is determined to meet quality standards. When quality standards are unclear, numerical standards are established through secondary tests such as stress and tension tests.
reporting
Create reports containing data, images, and charts generated during the responsiveness assessment and subsequent verification process.
solution
Processed materials and reports are delivered to the customer, and additional tests are carried out in a more optimized environment by creating a prototype system if necessary. Prototype verification is a work that must be carried out even after the start of a full-scale project, or can be preceded by the MATERIAL PROCESSING phase upon customer request.
Competence
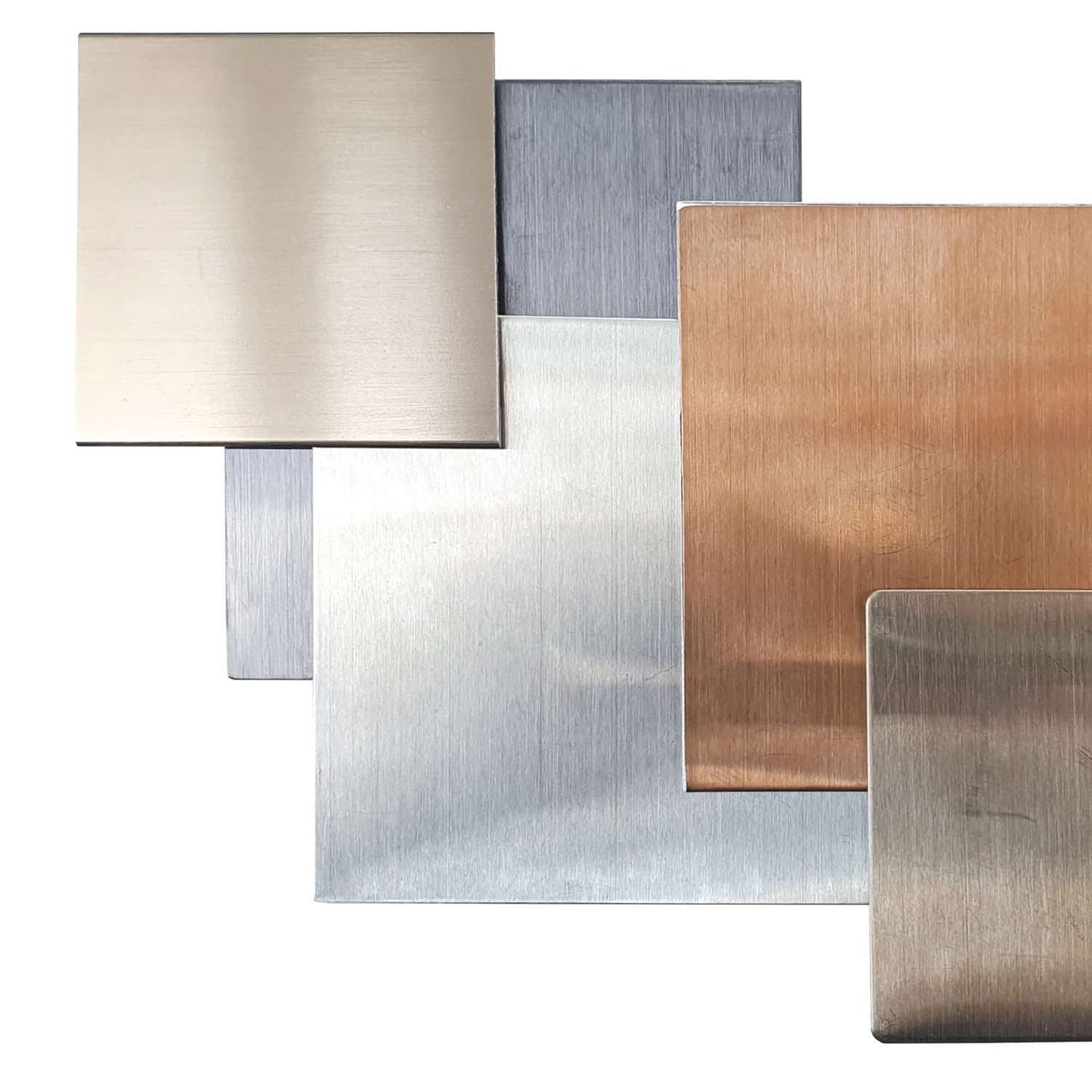
Material analysis
In order to select a laser with appropriate power and bandwidth and select functions that meet processing conditions, such as Operation Mode and Pulse Duration, an analysis of the processing materials must be performed first. As more customers use self-developed materials or composites, K2 is strengthening its ability to properly analyze and understand material properties.
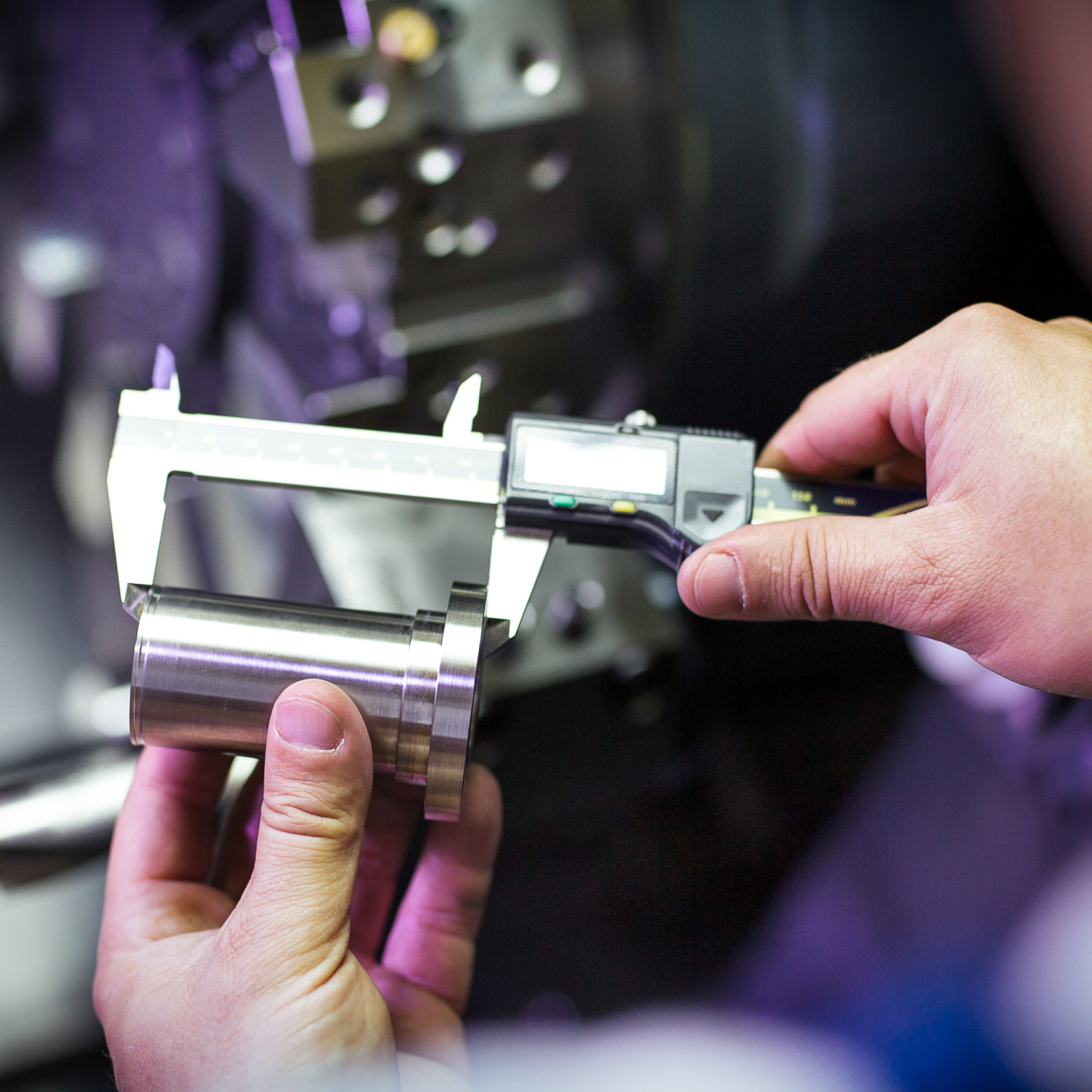
Shape analysis
Depending on the shape of the material, the transmission method of the beam generated by the laser module varies. If the shape of the material is three-dimensional or uneven, a 3D scanner instead of 2D can be considered, and a processing head can be used for equipment specialized in welding and cutting.
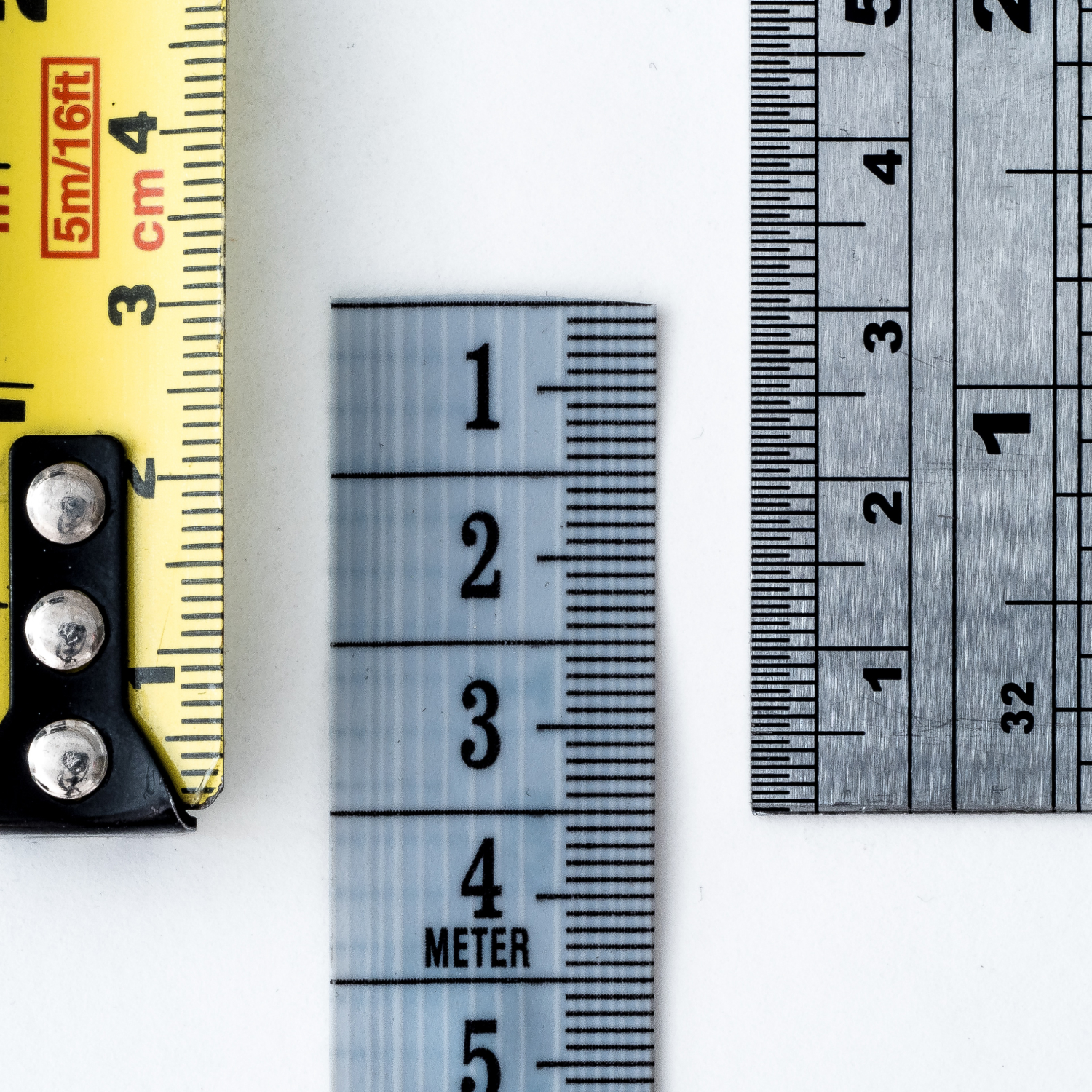
Capacity analysis
Depending on the size and volume of the material, adjustments such as Beam Delivery and Processing Sequence are required. Through capacity analysis, we explore ways to optimize factors that determine work time and yield, such as progress speed, number of processing times, and processing location and order.
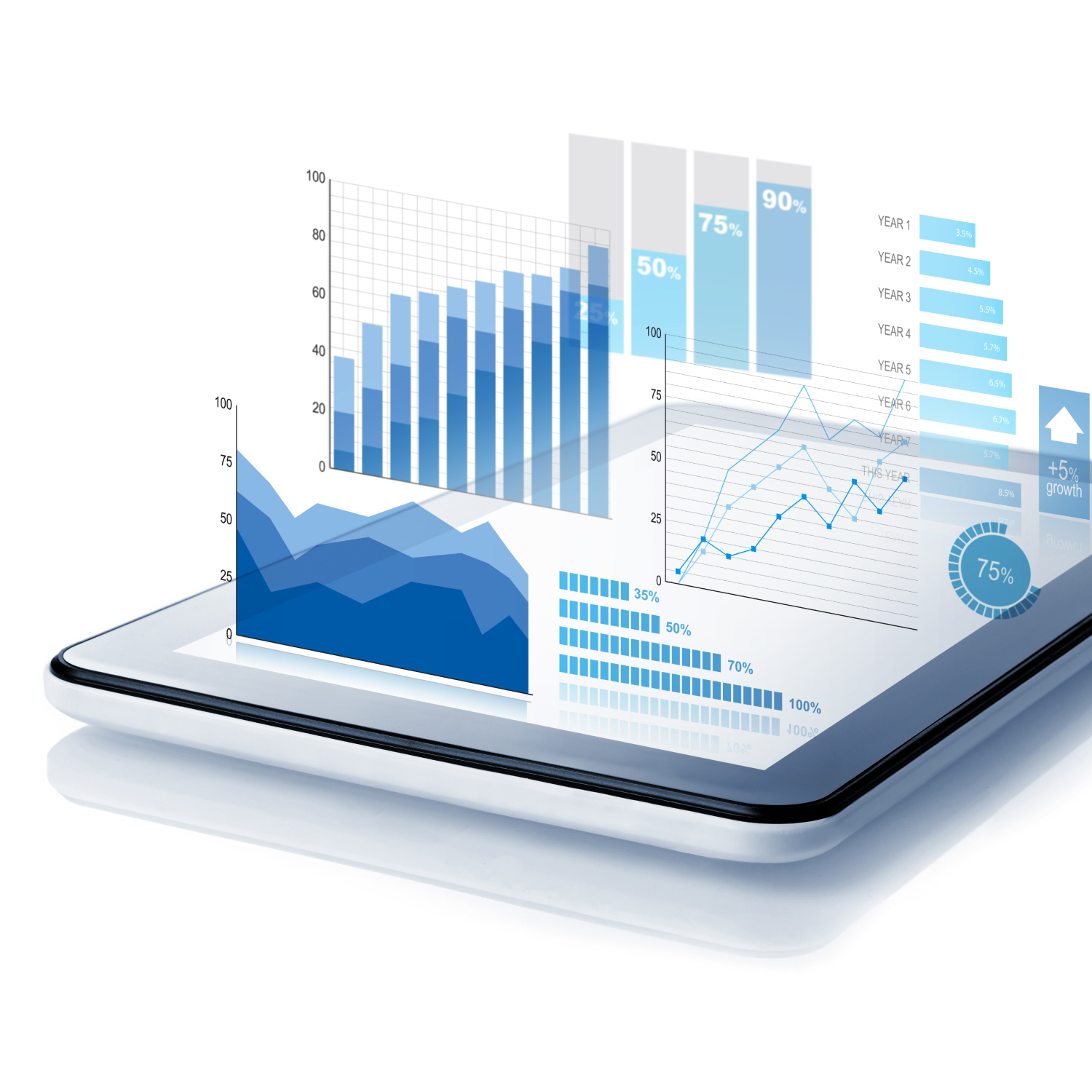
Condition analysis
If you consider the TRADE OFF between quality and cost, a design that is biased only towards quality misses practicality. K2 reviews various control methods in a complex manner so that quality can be achieved even with optimal system configuration and proper input of resources.