Laser drying
The slurry-coated coated foil passes through the drying facility while maintaining an appropriate tension to prevent drying. In the case of a convection dryer, the intensive travels at a speed of 35 to 80 meters per minute over a long path of up to 100 meters. As slurry moisture is slowly removed at a high temperature of 160 °C, active moisture settles on the surface, and a significant amount of energy is concentrated during this process. Laser drying systems with BEAM SHAPING technology can not only reduce the size of the facility to 10 meters, but also reduce energy consumption by up to 50%.
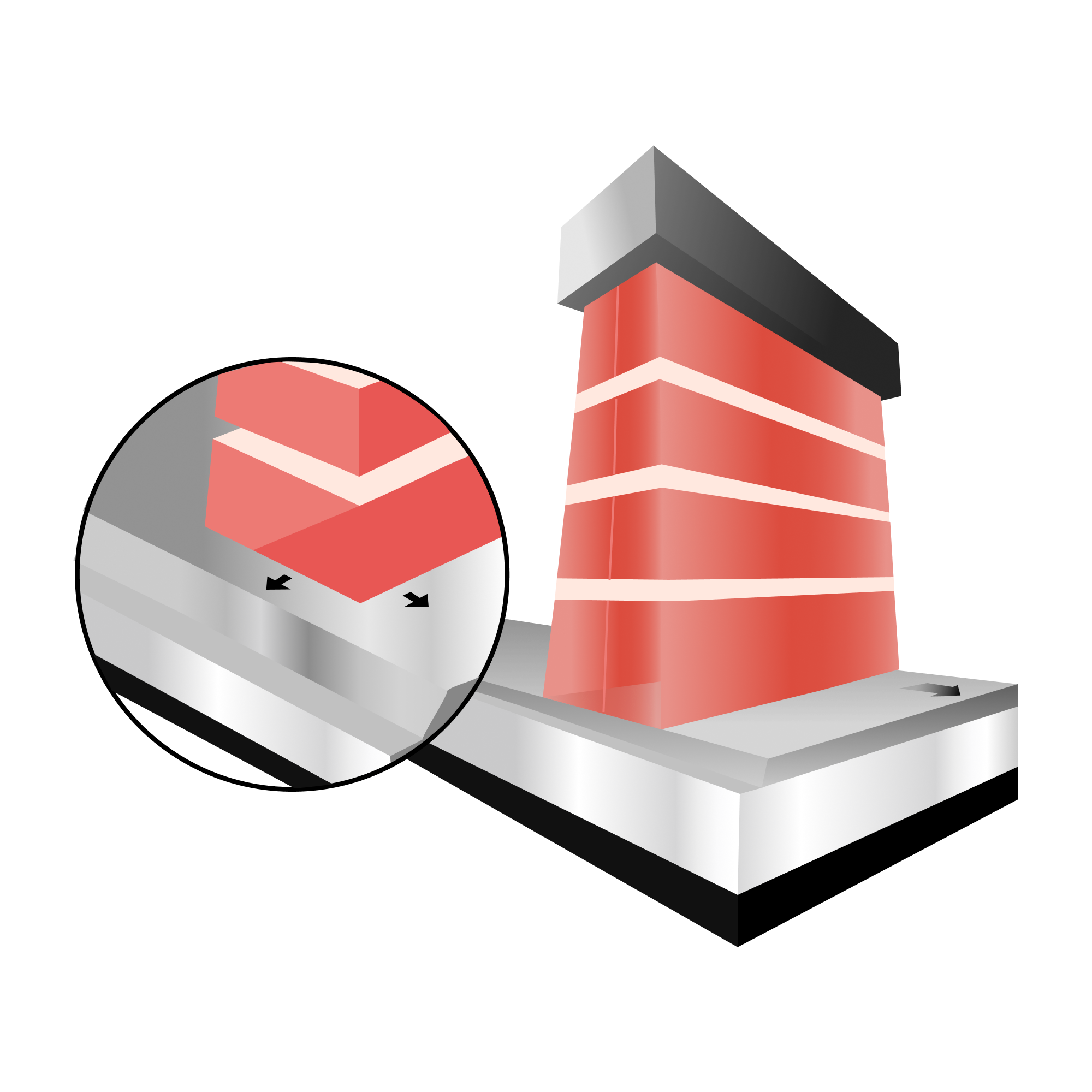
Features
availabilities
Due to the large size of convection drying plants, stabilizing the internal environment is very aggressive. Furious, it takes a lot of time to restart a device once it has been difficult. Lasers, on the Other Hand, can be flexible adjusted in processing cycles, so availability is high but limited is very short.
energy efficiency
As battery capacity drying, more intensive drying is required. The uniformly distributed laser beam transfers energy according to the thickness of the layer. Furrowth, the shape and size of the laser can be adjusted according to the width of the foil, reduced energy loss and reduced excitation.
Quality monitor
Process efficiency can be improved by adding additional lasers into convection currently in operation. The laser module, which is optimally structured to meet the diverse needs of customers, has a built-in vision and sensor for temperature measurement, and monitors the state of the material in real time.
availabilities
Due to the large size of convection drying plants, stabilizing the internal environment is very aggressive. Furious, it takes a lot of time to restart a device once it has been difficult. Lasers, on the Other Hand, can be flexible adjusted in processing cycles, so availability is high but limited is very short.
energy efficiency
As battery capacity drying, more intensive drying is required. The uniformly distributed laser beam transfers energy according to the thickness of the layer. Furrowth, the shape and size of the laser can be adjusted according to the width of the foil, reduced energy loss and reduced excitation.
Quality monitor
Process efficiency can be improved by adding additional lasers into convection currently in operation. The laser module, which is optimally structured to meet the diverse needs of customers, has a built-in vision and sensor for temperature measurement, and monitors the state of the material in real time.
25-50%
> 50%
99%
flexible
Core Technology
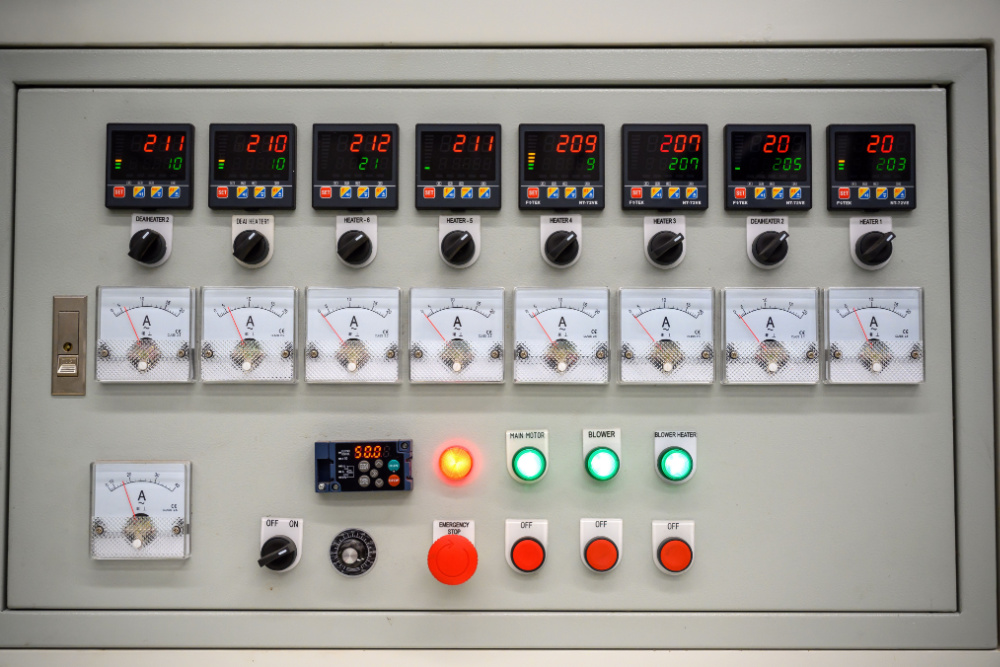
temperature control
Good quality electrodes cannot be easily irradiating high energy into a foil moving along a roll Excess energy causes rapid changes in materials, excessive cracking and clumping. Real-time precision monitoring is carried out with thermal imaging cameras and beam profiling technology so that the period during which the material remains constant at an appropriate temperature is lengthened.
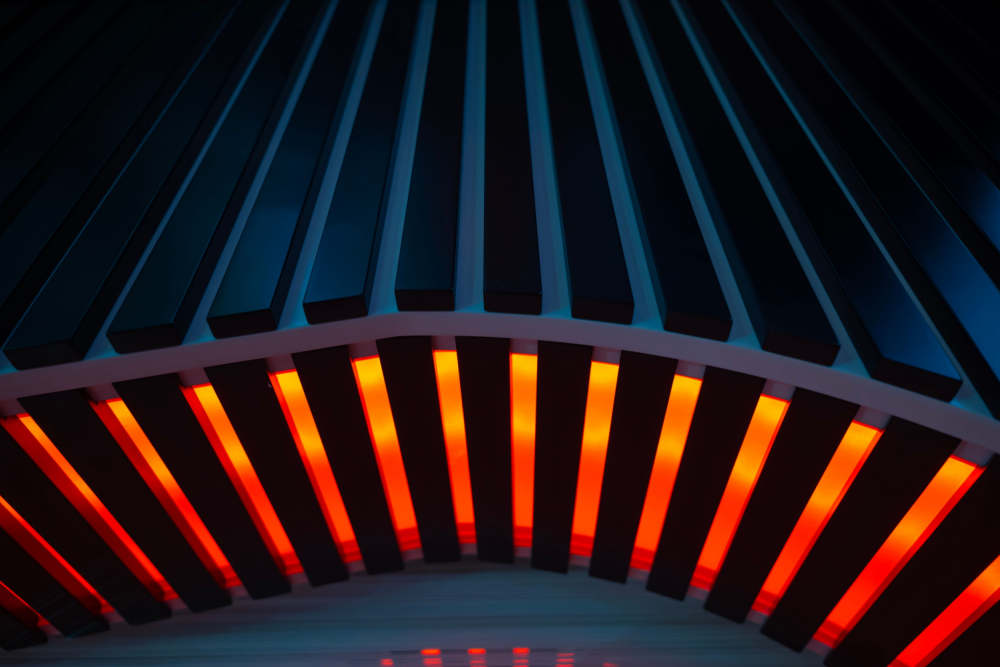
Hybrid solutions
The large amount of water vapor generated during the drying process interferes with the efficient transfer of energy. Unlike simple hot air or infrared drying, laser wavelengths absorb water vapor and moisture transfer the energy generated to the material. Furnitures, thanks to the reduced size of the facility, high-temperature steam and pollution can be managed more efficiently.
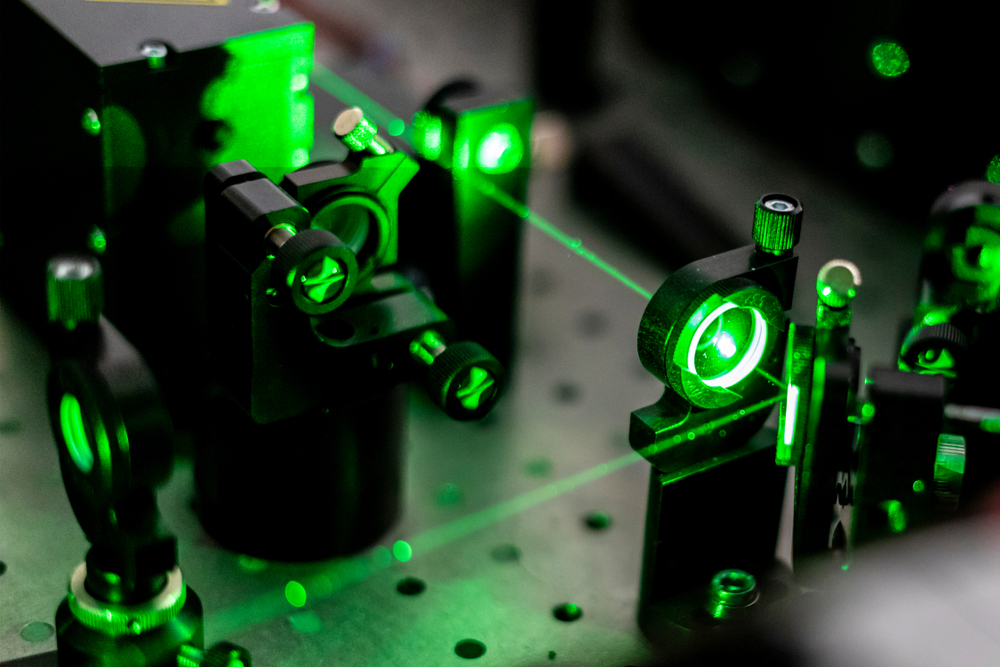
Dynamic beam
The core of laser drying is BEAM SHAPING TECHNOLOGY, which matches the shape of the BEAM to the shape and size of the coating. For example, if an effort is square but a laser is round, areas are created where energy is not sufficient properly or is excruciating. The K2 dryer with fiber laser, which can generate higher output energy than ordinary diodes, and excellent BEAM SHAPING motion.
Core Technology
Heading
Lorem ipsum dolor sit amet, consectetur adipiscing elit. Suspendisse varius enim in eros elementum tristique. Duis cursus, mi quis viverra ornare, eros dolor interdum nulla, ut commodo diam libero vitae erat. Aenean faucibus nibh et justo cursus id rutrum lorem imperdiet. Nunc ut sem vitae risus tristique posuere.
Heading
Lorem ipsum dolor sit amet, consectetur adipiscing elit. Suspendisse varius enim in eros elementum tristique. Duis cursus, mi quis viverra ornare, eros dolor interdum nulla, ut commodo diam libero vitae erat. Aenean faucibus nibh et justo cursus id rutrum lorem imperdiet. Nunc ut sem vitae risus tristique posuere.
Heading
Lorem ipsum dolor sit amet, consectetur adipiscing elit. Suspendisse varius enim in eros elementum tristique. Duis cursus, mi quis viverra ornare, eros dolor interdum nulla, ut commodo diam libero vitae erat. Aenean faucibus nibh et justo cursus id rutrum lorem imperdiet. Nunc ut sem vitae risus tristique posuere.
Heading
Lorem ipsum dolor sit amet, consectetur adipiscing elit. Suspendisse varius enim in eros elementum tristique. Duis cursus, mi quis viverra ornare, eros dolor interdum nulla, ut commodo diam libero vitae erat. Aenean faucibus nibh et justo cursus id rutrum lorem imperdiet. Nunc ut sem vitae risus tristique posuere.